As one of the largest diesel engine manufacturers in the world, Cummins’ products are widely used in industries such as mining, construction, agriculture, and transportation.
While Cummins is known for its high reliability and durability, it’s possible that Cummins diesel engine won’t start. When the engine fails to start, it not only affects the normal operation of the equipment but can also result in significant costs.
In this article, we will delve into the common causes of Cummins engine failures in depth and provide effective troubleshooting and solutions to help users quickly regain operational efficiency.
Part 1. Why is Cummins Diesel Engine Not Starting?
Understanding the common starting issues of Cummins engines and their causes can help prevent problems in advance, ensuring the engine runs smoothly and efficiently. By identifying potential issues early, you can minimize unexpected downtime, lower repair costs, and extend the lifespan of your equipment.
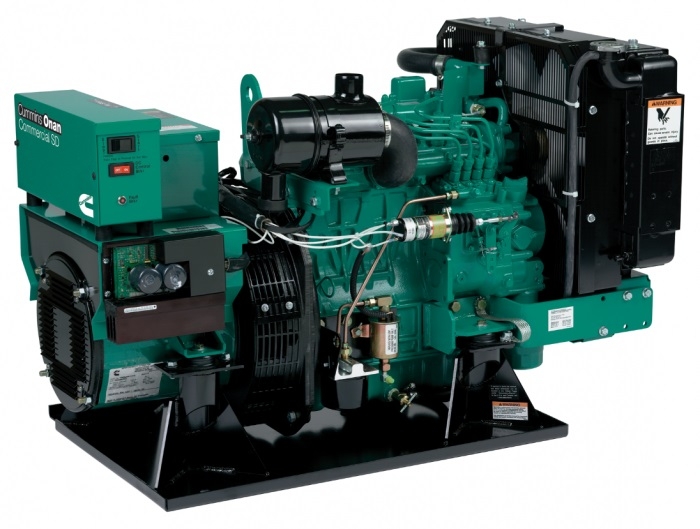
Here we will analyze the main causes of starting problems in Cummins engines and troubleshooting tips in detail.
1. Battery Issues
A common cause of a Cummins diesel engine not starting is a weak or dead battery. Diesel engines require a significant amount of power to start, and even a slightly low battery voltage can hinder the start process.
Battery faults or low voltage often result in inadequate current supply, causing the engine to start but not running properly, resulting in a failed start.
Troubleshooting Tips:
- Check the battery voltage with a multimeter. A fully charged battery should read around 12.6 to 12.8 volts.
- Check the battery terminals for corrosion and make sure the connections are tight.
2. Fuel System Problems
Fuel delivery is crucial for the proper functioning of a diesel engine. If the fuel filter is clogged or the fuel tank is empty, fuel may not flow smoothly to the engine, which leads to a failed start. Therefore, ensuring proper fuel system operation is crucial for the engine to start effectively.
Troubleshooting Tips:
- Make sure your fuel tank has diesel.
- Replace clogged fuel filters.
- Bleed the fuel system to remove any trapped air.
3. Faulty Starter Motor
If your engine completely fails to start, the issue may lie with the starter motor. A faulty starter motor may not produce enough torque to successfully start the engine. Therefore, checking whether the starter motor is damaged or malfunctioning is a crucial step in resolving starting issues.
Troubleshooting Tips:
- Test the starter motor by listening for a clicking sound when you turn the key. If you hear this, the starter may be bad.
- Check the starter relay and wiring for damage.
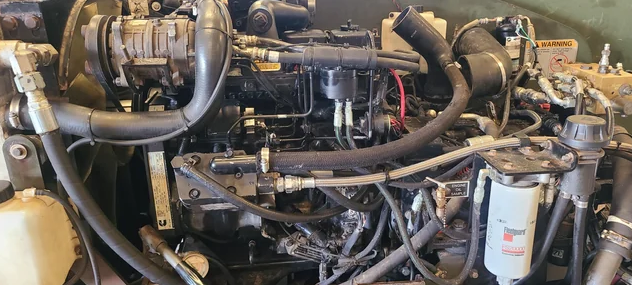
4. Glow Plug or Heater Grid Issues
In cold weather, diesel engines rely on glow plugs or heater grids to warm the combustion chamber and help start the engine smoothly. If these components fail, particularly in low temperatures, the engine may experience difficulty starting.
Effective heating is crucial for ensuring the engine starting properly in cold weather, so it is important to regularly check the condition of the glow plugs and heater grids.
Troubleshooting Tips:
- Test the starter motor by listening for a clicking sound when you turn the key. If you hear this, the starter may be bad.
- Check the starter relay and wiring for damage.
5. Air Intake Problems
If the air filter or sensors in the intake system are clogged or malfunctioning, it could prevent the Cummins diesel engine from starting. Blockages in the air filter or sensors can limit the amount of air the engine can intake, affecting its starting performance.
Ensuring the proper functioning of the intake system is crucial for a smooth engine start, so it is important to regularly inspect and maintain these components.
Troubleshooting Tips:
- Check and clean the air filter.
- Check the intake system for any obstructions or damage.
- Use a diagnostic tool to check for sensor faults in the intake system.
6. Low Compression
Diesel engines rely on high compression ratios to ignite fuel. If piston rings are damaged or valves are worn, resulting in insufficient compression in one or more cylinders, the engine may experience difficulty starting.
Low compression affects the fuel ignition process, preventing the engine from starting properly. Therefore, ensuring that cylinder compression is within the normal range is crucial for ensuring reliable engine starting.
Troubleshooting Tips:
- Perform a compression test to identify any issues with compression.
- If low compression is detected, you may need to rebuild or replace engine components.
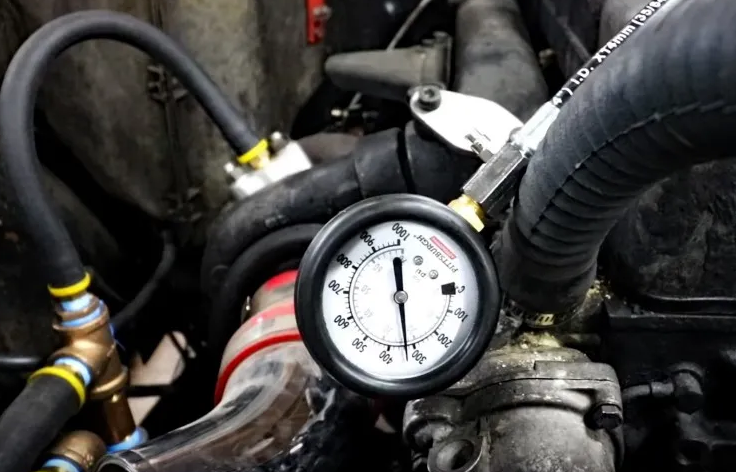
7. Electrical and Sensor Failures
Modern Cummins diesel engines are equipped with various sensors to monitor fuel, air, and engine conditions. Critical sensors, such as the crankshaft position sensor and camshaft position sensor, can prevent the engine from starting if they fail.
The proper functioning of these sensors is essential for ensuring a smooth engine start and stable operation. Therefore, regularly checking the condition of these sensors is crucial for maintaining engine reliability.
Troubleshooting Tips:
- Scan the engine for error codes using an OBD-II diagnostic tool. For instance, codes like P0335 (Crankshaft Position Sensor) or P0340 (Camshaft Position Sensor) can point to issues preventing your engine from starting.
Part 2. Effective Way to Fix Cummins Diesel Engine Not Starting
In the previous sections, we covered the common causes of Cummins diesel engine failures and provided corresponding troubleshooting tips. Besides these tips, here is an highly effective solution for restarting a Cummins diesel engine, which is spring starter. It can help the engine start successfully and quickly.
How Spring Starter Can Help in Cummins Diesel Engine Starting?
Spring starter stores mechanical energy by winding a spring, releasing this stored energy to provide the required torque to start the engine.
It does not rely on battery or electrical systems, making it highly effective for starting engines when the diesel engine battery is low on power, unable to provide enough electricity, or when the electric starter system is faulty, or in remote or harsh environments.
Benefits of Using Spring Starter
There are many spring starters available on the market. Here, we will take Cqstart spring starter as an example to detail its specific advantages, helping you fully understand the unique benefits and appeal of using a spring starter to start a diesel engine.
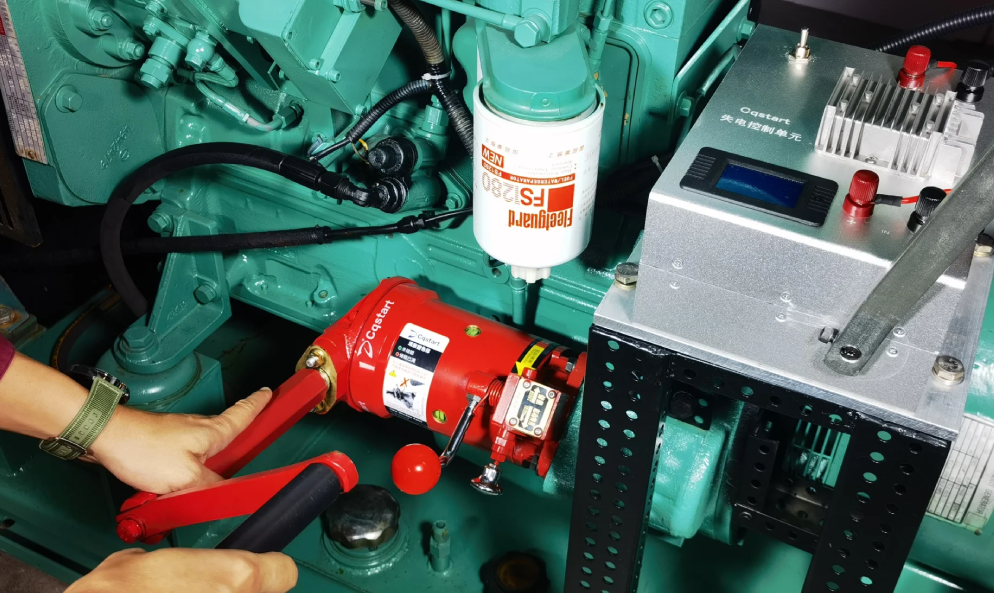
1. Suitable for Extreme Environments
Spring starter is designed to withstand both high and low temperatures, with minimal impact on its performance from environmental conditions. This allows the spring starter to operate effectively even in extreme environments, which is crucial for maintaining the normal operation of diesel engines under harsh conditions.
2. Safety
Spring starter undergoes a pre-engagement process and has natural anti-explosion features, making it suitable for hazardous environments.
This design ensures that no accidental explosions or fires occur during the starting process, greatly enhancing operational safety. It is especially valuable in work environments with flammable materials or chemicals, ensuring the safe startup of diesel engines.
3. High Quality
Every spring starter undergoes rigorous testing and is equipped with waterproof, oil-resistant, salt fog-resistant, and corrosion-resistant capabilities.
Whether in humid marine environments or oil-heavy industrial settings, spring starter operates reliably, ensuring that diesel engines can be started consistently under various environmental conditions.
4. Ease of Operation
Spring starter uses a standard SAE mounting system, requiring only screws for installation. A typical operation cycle takes 30 seconds, while smaller models can start as little as 10 seconds.
This fast and simple process not only improves work efficiency, but also reduces maintenance and startup time, making troubleshooting for diesel engines much more efficient.
5. Cost-Effective
Spring starters don’t require extra systems like air tanks or pipelines, making their overall cost lower than many other types of starters.
This high cost-effectiveness enables significant long-term savings while still providing reliable starting performance. It is particularly suitable for applications where efficient and cost-effective solutions are required.
Part 3. Tips for Caring Your Diesel Engine
To ensure efficient operation of Cummins diesel engines in the long term, some preventive maintenance is necessary. With regular maintenance, you can prevent potential issues from turning into major failures, reduce unexpected downtime, and extend the engine’s lifespan. Let’s explore the key preventive measures.
1. Regular Change Oil & Oil Filter
Oil is crucial for the performance of a Cummins diesel engine as it helps lubricate and cool internal components. Regularly changing the oil and oil filter ensures the engine runs optimally and prevents wear caused by contaminated or degraded oil.
2. Check & Replace Air Filter
Air filter prevents dust and debris from entering the engine. Regularly inspecting and replacing the air filter as needed ensures that the engine receives enough clean air, improving combustion efficiency and preventing carbon buildup.
3. Check Electrical System
Regularly check the starting system, battery, and cable connections to ensure that there are no signs of corrosion, looseness, or damage. For Cummins diesel engines operating in harsh environments, insufficient battery power or electrical system faults can lead to starting issues. Therefore, maintaining these components in good condition is crucial for ensuring reliable engine performance.
4. Fuel System Maintenance
Diesel engines have high demands for fuel cleanliness, so it is crucial to regularly replace the fuel filter and check for leaks in the fuel lines. This helps prevent fuel contamination, ensures proper fuel delivery, and avoids issues such as starting difficulties or power loss.
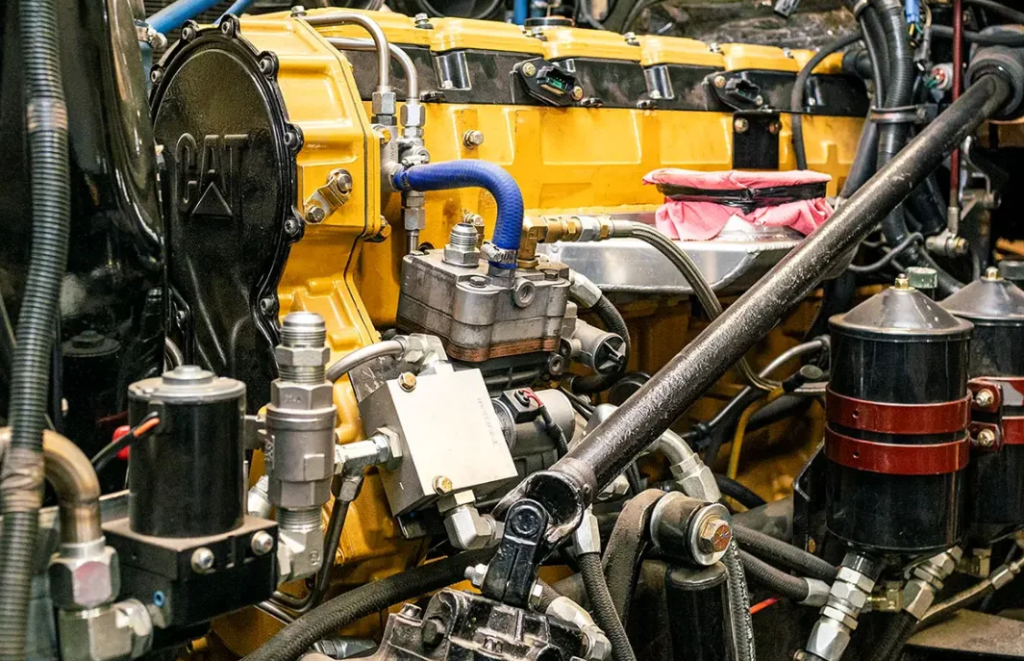
5. Cooling System Maintenance
The condition of the coolant is crucial for regulating the engine temperature. Regularly check the coolant level, concentration, and inspect the radiator and cooling hoses for leaks. Timely replacement of the coolant helps prevent engine overheating and avoids damage to components caused by excessive heat.
6. Check Exhaust System
Regularly check the exhaust system connections to ensure they are secure and inspect the exhaust pipes for blockages or cracks. This prevents harmful exhaust gases from backflowing or leaking and ensures proper exhaust flow. Maintaining a well-functioning exhaust system helps uphold emission standards and fuel efficiency.
7. Perform Diagnostic Tests
Regular diagnostic testing with specialized equipment effectively monitors the engine’s operational status and helps identify potential issues early. Diagnostic tests can pinpoint sensor failures, fuel injection problems, and other hidden faults, allowing for timely interventions and maintenance.
Final Thoughts
There could be many reasons why a Cummins diesel engine fails to start, including simple battery issues to more complex faults. By identifying these potential causes and following the troubleshooting tips outlined in this article, you can usually resolve the issue on your own.
Additionally, spring starters can be an effective solution. If after following these steps, your Cummins engine still won’t start, it ‘s best to contact a professional mechanic or Cummins customer support for further assistance.
FAQs about Diesel Engine Not Start
1. Why is diesel engine turning but not starting?
If a diesel engine turns over but doesn’t start, it often points to issues such as fuel delivery problems, low compression, or electrical system faults. Checking the fuel system, compression levels, and electrical components can help diagnose and fix the problem.
2. How do you diagnose a diesel engine not starting?
To diagnose a diesel engine that won’t start, check the battery, starter motor, fuel system, and compression. Ensure all electrical components are functioning properly. This approach will help identify the issue.
3. How to know if diesel starter is bad?
To determine if a diesel starter is bad, listen for unusual clicking sounds when you attempt to start the engine, or if the engine cranks slowly or not at all despite a fully charged battery.
You can also test the starter with a multimeter to check for proper voltage and amperage. If the starter motor shows signs of overheating, excessive wear, or fails to engage, it may need to be replaced.