Diesel engines are widely used in agriculture, logistics, marine, and many other industries, serving as the core power source for various equipment. When a diesel engine encounters problems, it can lead to equipment downtime, production delays, and even financial losses. Therefore, quickly and accurately diagnosing engine issues is crucial.
But how do you diagnose a diesel engine problem?
Don’t worry! Here we will provide a comprehensive guide to diagnosing diesel engine problems, helping you identify the root cause of the issue and resolve it promptly.
Part 1. Common Diesel Engine Problems & Solutions
1. Hard Starting or Failure to Start
Symptoms: The diesel engine cranks slowly or fails to crank at all. Sometimes, it’s turning over but not starting.
Causes:
- Weak or Dead Battery: Insufficient power for the starter motor to turn the engine.
- Faulty Starter Motor: A worn or damaged starter motor may not engage the engine properly.
- Fuel System Issues: Clogged fuel filters, air in fuel lines, or a failing fuel pump can prevent proper fuel delivery.
- Low Compression: Worn piston rings or valve seats reduce the engine’s ability to ignite fuel.
- Cold Weather: Thickened oil or gelled diesel fuel can make starting harder.
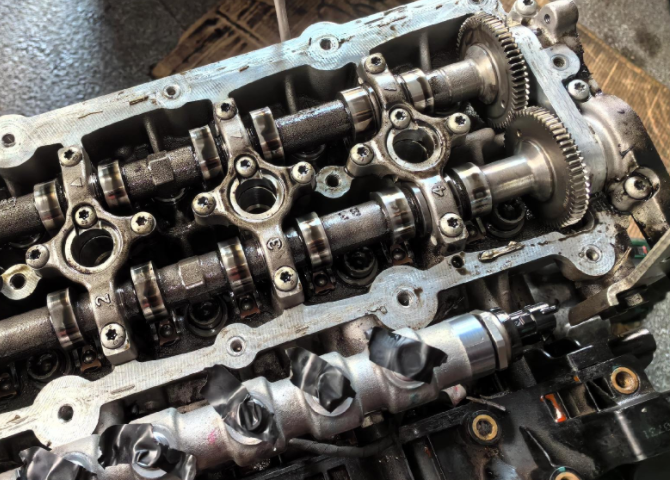
Solutions:
- Test the battery voltage and charge or replace it if necessary.
- Inspect the starter motor for wear or damage and repair or replace it.
- Bleed air from the fuel lines, replace clogged filters, and test the fuel pump.
- Use synthetic oil and fuel additives designed for cold temperatures.
- If the diesel engine has difficulty starting but the electrical system (such as the battery and starter) is functioning properly, you can try spring starter.
Why Use Spring Starter?
No Electrical Power Needed: It relies on mechanical energy from a wound spring, making it perfect when batteries are weak or drained.
Works in Extreme Conditions: Unlike electric starters, Spring Starters perform well in cold or harsh environments where electrical systems might fail.
Durability and Reliability: With fewer electrical parts, Spring Starters are less prone to failure and easier to maintain.
Cost-Effective: Low maintenance and minimal repair costs make it a cost-effective solution in remote areas or where electricity is unreliable.
2. Excessive Smoke from the Exhaust
Symptoms: Noticeable black, blue, or white smoke coming from the exhaust, often with a distinct smell.
Causes:
Black Smoke:
- Over-fueling due to malfunctioning injectors or incorrect timing.
- Clogged air filters are restricting air flow.
- Malfunctioning turbocharger leading to inefficient combustion.
Blue Smoke:
Engine oil entering the combustion chamber because of worn piston rings, damaged valve seals, or a failing turbocharger seal.
White Smoke:
Unburned fuel caused by low compression, bad injectors, or extremely cold weather.
Coolant leaking into the combustion chamber due to a blown head gasket.
Solutions:
- Replace faulty injectors, clean or replace air filters, and check the turbocharger’s operation.
- Repair or replace worn piston rings, valve seals, or turbo seals for blue smoke.
- Address compression issues, repair leaking gaskets, and test injectors for white smoke.
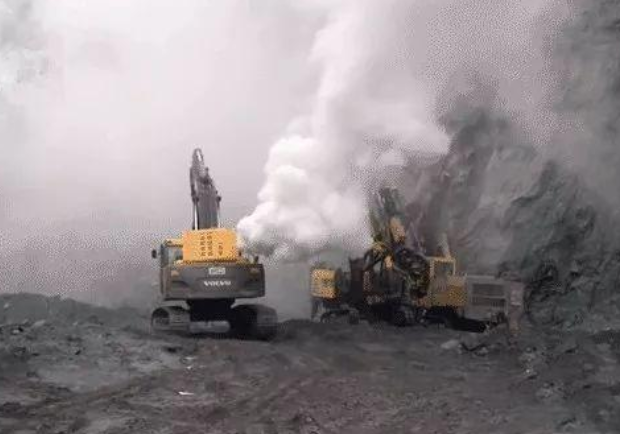
3. Loss of Power or Poor Performance
Symptoms: The engine struggles to accelerate, maintain speed, or perform under heavy loads.
Causes:
- Dirty Fuel Injectors: Improper spray patterns reduce combustion efficiency.
- Clogged Fuel Filters: Restrict fuel flow, leading to inadequate power delivery.
- Restricted Air Intake: Clogged air filters or damaged intake components limit airflow.
- Turbocharger Failure: Reduced boost pressure results in power loss.
- Exhaust Restrictions: Blockages in the exhaust system cause back pressure, reducing performance.
Solutions:
- Clean or replace injectors, fuel filters, and air filters.
- Inspect and service the turbocharger and exhaust system for blockages or damage.
4. Engine Overheating
Symptoms: The temperature gauge rises above normal, or you notice steam and boiling coolant.
Causes:
- Low Coolant Levels: Leaks in the radiator, hoses, or water pump cause insufficient cooling.
- Faulty Thermostat: Stuck closed, it prevents coolant from circulating.
- Blocked Radiator: Debris or mineral deposits reduce cooling efficiency.
- Failed Water Pump: A broken impeller or belt prevents proper coolant flow.
- Heavy Load or Extreme Heat: Additional strain on the cooling system exacerbates issues.
Solutions:
- Top off coolant levels and repair leaks in hoses, radiators, or the water pump.
- Replace a malfunctioning thermostat or clean a blocked radiator.
- Inspect the water pump and cooling fan for proper operation.
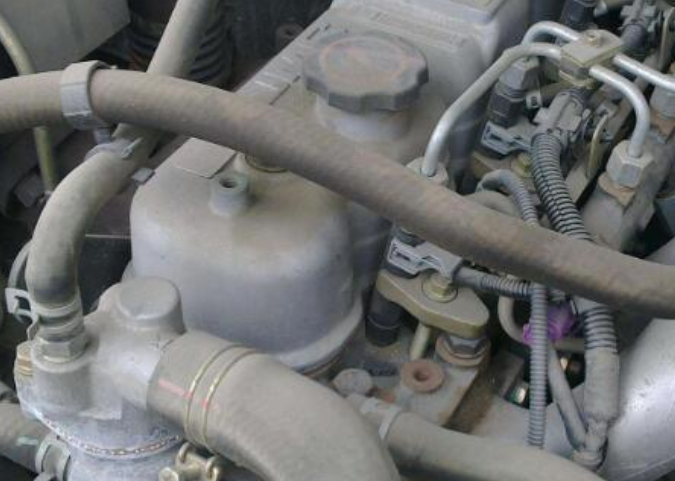
5. Unusual Noises During Operation
Symptoms: Knocking, hissing, rattling, or whistling sounds from the engine.
Causes:
- Knocking: Caused by incorrect fuel injection timing, poor-quality fuel, or carbon buildup in the combustion chamber.
- Hissing: Indicates air leaks in the intake system or a leaking exhaust manifold.
- Rattling: Loose components such as belts, pulleys, or mounts can cause vibrations and noise.
- Whistling: Points to a damaged turbocharger or a loose belt.
Solutions:
- Adjust fuel injection timing and use high-quality fuel to address knocking.
- Locate and repair air or exhaust leaks causing hissing sounds.
- Tighten or replace loose components and inspect the turbocharger for damage.
Part 2. How to Diagnose Diesel Engine Problems?
When diagnosing diesel engine problems, using modern diagnostic tools can greatly improve efficiency and help technicians quickly and accurately identify and resolve issues.
Here are some commonly used modern diagnostic tools that you may find helpful to familiarize yourself with in case they come in handy someday.
1. OBD Diagnostic Tool
OBD (On-Board Diagnostics) diagnostic tool is widely used for diagnosing modern diesel engine problems by connecting to the vehicle’s on-board diagnostic system (OBD-II) and the Engine Control Unit (ECU). It reads the engine fault codes (DTCs) to help technicians quickly identify problems.
Diagnostic Function: In addition to reading fault codes, the OBD tool can display real-time engine data such as engine speed, intake temperature, oil pressure, and oxygen sensor readings. These data help diagnose engine performance and conditions, pinpointing potential faulty components.
Advantages: Using an OBD diagnostic tool allows for quick identification of issues and provides specific fault codes, avoiding traditional trial-and-error diagnostic methods and reducing unnecessary downtime. It is especially important for identifying electronic system issues such as sensor or fuel injection system malfunctions.
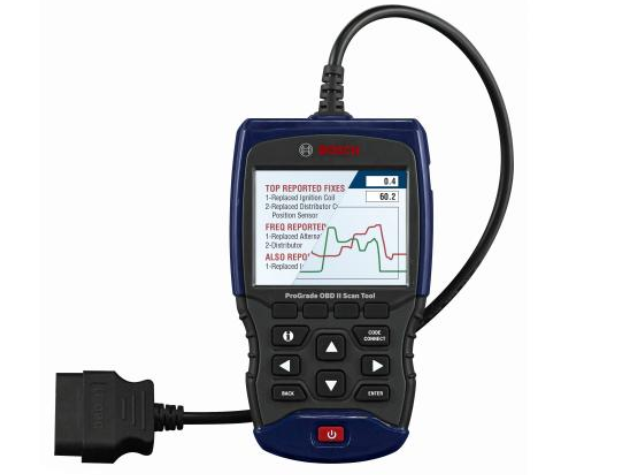
2. Pressure Tester
Pressure tester is a tool used to measure the pressure of the diesel engine’s fuel injection system, which is crucial for diagnosing issues with injectors, fuel pumps, and fuel lines.
The pressure in the fuel system is vital for the engine’s proper operation, and abnormal pressure can lead to power loss or difficulty starting.
Diagnostic Function: The pressure tester can detect whether the fuel pump provides sufficient pressure, check whether the injectors spray properly, and determine if there are issues such as blockages, damage, or uneven pressure. It can also help identify leaks in the fuel system.
Advantages: By testing the fuel system’s operating pressure with a pressure tester, technicians can quickly locate faults in components such as injectors and fuel pumps, avoiding unnecessary disassembly. It also helps determine whether the fuel supply is normal, preventing fuel-related issues from preventing engine startup or causing instability.
3. Cylinder Pressure Gauge
Cylinder pressure gauge is used to measure the compression pressure in the diesel engine’s cylinders, which is a key tool for determining the engine’s sealing integrity and overall performance.
The compression pressure directly affects the engine’s combustion efficiency, power output, and starting performance.
Diagnostic Function: The cylinder pressure gauge helps diagnose cylinder sealing issues. If the compression pressure is low, further inspection of components like the cylinder gasket, piston rings, and valves is necessary to determine whether replacement or repair is needed. It can also detect pressure differences between cylinders, helping identify specific cylinder faults.
Advantages: The cylinder pressure gauge is a precise diagnostic tool that helps determine whether there are cylinder damage or compression issues. Using this tool allows technicians to avoid unnecessary disassembly and accurately determine whether the engine requires major repairs or just minor adjustments, saving time and costs.
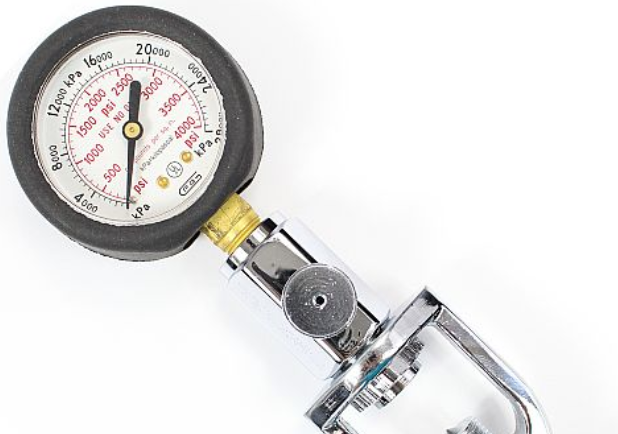
Part 3. Final Thoughts
Diagnosing diesel engine problems requires a combination of observation, basic checks, and systematic analysis. With the right tools, preventive maintenance, and high-quality parts, you can effectively resolve issues and extend the life of your engine. If your diesel engine is hard to start but the electrical system is still functioning, don’t forget to try spring starter.
Part 4. FAQs about Diagnose Diesel Engine Problems
How to tell if a diesel engine is bad?
A diesel engine may be bad if it has trouble starting, emits unusual smoke, loses power, makes strange noises, overheats, or shows poor fuel efficiency. These signs often indicate internal issues or system malfunctions that need attention.
Is it worth rebuilding a diesel engine?
Rebuilding a diesel engine is worth it if the damage is manageable and the repair costs are lower than replacing it. If the engine is old or severely damaged, replacing it may be more cost-effective.
How many miles on a diesel engine is bad?
A diesel engine is generally considered to be in bad condition after around 500,000 to 700,000 miles, although this can vary depending on maintenance and usage. Engines that have been well-maintained may last longer, while poor maintenance or harsh conditions can cause issues earlier. Regular maintenance is crucial in extending the lifespan of a diesel engine.
Why is my diesel engine struggling to accelerate while?
If your diesel engine is struggling to accelerate, it could be due to clogged fuel filters, a failing fuel pump, air intake issues, or problems with the turbocharger or injectors. A clogged diesel particulate filter (DPF) can also limit acceleration. Regular maintenance helps identify the problem.