As an important part of the diesel engine, the diesel engine starter plays a very important role. Among all starters, the most widely used ones are electric starters, spring starters, and hydraulic motors. Many people have a doubt: With hydraulic motors, air motors, and other high-tech products, why are spring starters still popular? Today we will compare the difference between a spring starter and a hydraulic motor. Through this comparison, you can more clearly realize the importance of spring starters.The general classification of spring starters.
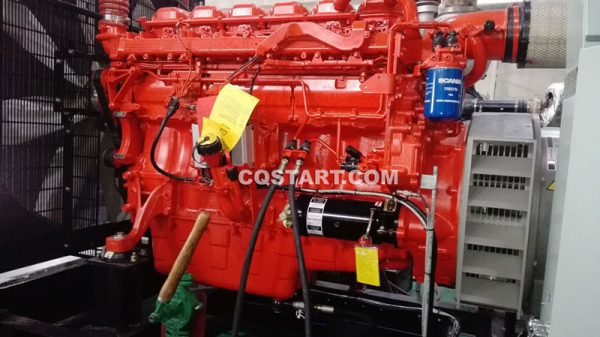
How does it work? Spring starter VS hydraulic motor
Working principle of spring starter
The spring-powered motor uses a disc spring as the energy storage medium. It only uses manual rotation to compress the spring, and then instantly releases the torque and speed to the diesel flywheel to start the engine without energy consumption and emission pollution.
It is installed on the diesel engine in a standard way, without the need for batteries, compressed air tanks, or hydraulic drives, as well as control valves, cables, etc.
The spring starter adopts a cavity and transmission mechanism made of a special alloy. The unique and concise structural design makes it so that it does not produce sparks or radiation during use. It has a solid and reliable structural performance and is suitable for spark-sensitive or difficult-to-implement equipment maintenance. occasion.
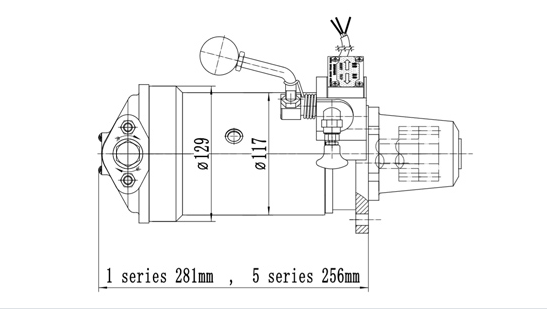
Working principle of hydraulic starter
Through the charging device, the hydraulic oil is squeezed into the accumulator. When sufficient pressure is reached, the high-pressure hydraulic oil in the accumulator is released to drive the hydraulic starter motor so that the gear of the starter motor meshes with the flywheel ring gear, and the output is sufficient The torque drives the flywheel ring gear of the diesel engine, to realize the process of starting the ignition of the diesel engine.
A basic IPU diesel engine hydraulic starting system should include the fuel tank, hydraulic starting motor, manual charging device, filter, pressure gauge, accumulator, control valve.
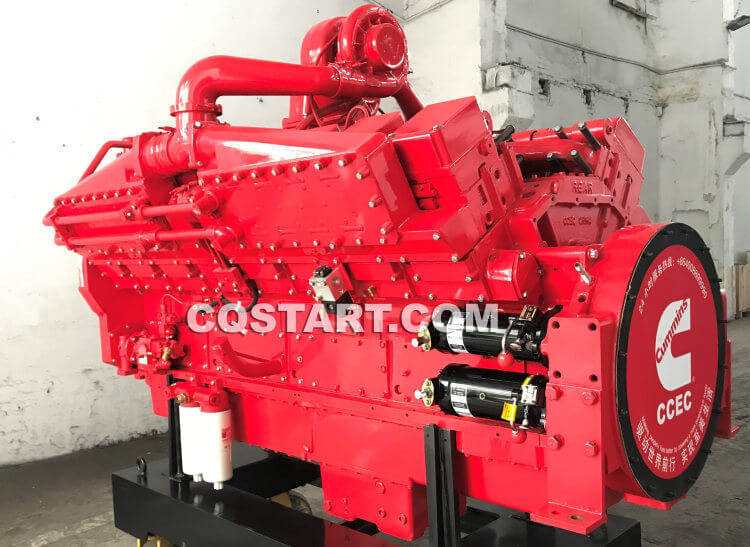
Application: Spring starter vs hydraulic motor
Application of spring starter
General industrial use: standby and replacement of other start-up systems. Installed inland and marine diesel generator sets, mining machinery, engineering machinery, and agricultural irrigation and drainage machinery.
Special environment: coal mines, oil fields, and chemical plants, etc.
Emergency conditions: fire fighting equipment and lifeboats, military use.
Application of hydraulic motor
Hydraulic motors, also known as oil motors, are mainly used in injection molding machinery, ships, hoists, construction machinery, construction machinery, coal mining machinery, mining machinery, metallurgical machinery, ship machinery, petrochemicals, port machinery, etc.
The high-speed motor gear motor has the advantages of small size, lightweight, simple structure, good manufacturability, insensitivity to oil pollution, impact resistance, and low inertia. Disadvantages include large torque pulsation, low efficiency, small starting torque (only 60%-70% of rated torque), and poor low-speed stability.
Features: spring starter VS hydraulic motor
Features of spring starter
- The spring starter can meet the cold start requirements of the diesel engine, and can excellently complete the start task of the full load state.
- Starter installation complies with SAE standards
- The direction of the rotating shaft head can be adjusted to the best manpower rotating angle
- It can adapt to the needs of different diesel engines, and the superb material processing technology can ensure its long service life, and it can adapt to different working environments. The severe cold area requires an auxiliary engine starting device.
Features of hydraulic motors
From the perspective of energy conversion, hydraulic pumps and hydraulic motors are hydraulic components that work reversibly. Inputting working fluid to any hydraulic pump can turn it into a hydraulic motor working condition; on the contrary, when the main shaft of the hydraulic motor is removed from the outside When the torque is driven to rotate, it can also be changed to the working condition of the hydraulic pump. Because they have the same basic structural elements-airtight but cyclically variable volume and corresponding oil distribution mechanism.
However, due to the different working conditions of hydraulic motors and hydraulic pumps, their performance requirements are different, so there are still many differences between hydraulic motors and hydraulic pumps of the same type. First of all, the hydraulic motor should be capable of forward and reverse rotation, so its internal structure is required to be symmetrical; the speed range of the hydraulic motor needs to be large enough, especially for its minimum stable speed.
Therefore, it usually uses rolling bearings or hydrostatic sliding bearings; secondly, because the hydraulic motor works under the condition of input pressure oil, it does not need to have the self-priming ability, but it needs a certain initial seal to provide the necessary starting torque. Because of these differences, hydraulic motors and hydraulic pumps are similar in structure, but they cannot work reversibly.
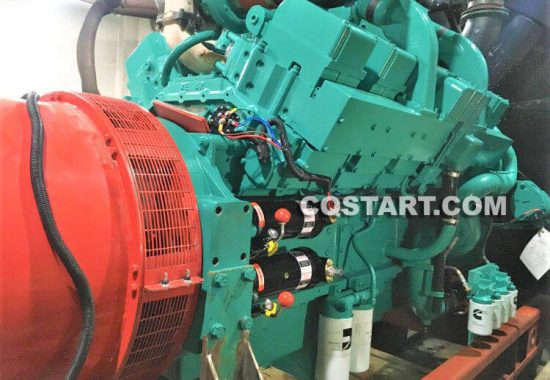
By comparison, we can find that spring starters generally exist as backup starters. Its existence is more like a Plan B. It can work more stably when most other launchers can’t work normally. Therefore, although it requires manpower to start, it has been loved by many customers.